Should Maintenance Be Performed on a Routine Basis?
It is commonly thought that, once a cable leak has been found and fixed, the cable will be safe from moisture. After a repair, there is a natural tendency to conclude that everything is okay and that maintenance can be ignored until more leaks are found on the cable. This couldn't be further from the truth.Maintaining a reliable cable plant is something like maintaining a large building. Deterioration of the building must be taken seriously, especially the roof, which should be frequently repaired to ensure extended use. Several parts of the country experience long periods of dry weather where structures are not subjected to water damage. There's no problem for buildings (and cables) when it doesn't rain, but after extended periods of neglect, they both require constant attention to fend off the water problems when the storms come. Maintenance is best performed when the weather's dry.
Today, this type of routine maintenance is often called proactive maintenance. Many telephone companies are shifting toward a proactive approach to the outside plant in order to prevent subscriber calls, Public Utilities Commission (PUC) complaints, and even catastrophic failure. It's preventive medicine for the outside plant. Rather than treating the outcome of poor health (big leaks and low delivery pressure), a good diet and exercise program (changing out old cable/devices and performing maintenance on the problematic routes first) will keep future problems from occurring.
Are Cable Leaks Hard to Find? When looking for leaks, an entire cable cannot be held under water (like a tire tube) to look for bubbles at the point of damage. You have to devise another method. Pressure readings will tell you that a cable is losing air, but they don't tell you where. Because there is an inherent amount of air flow in pressurized cables, the best scheme is to follow the air flow to the leak. By setting up check points and using devices to measure the air flow, the leak can be quickly located without a foot-by-foot examination of the cable.
To use another analogy, let's say we're transporting money between two points (Checkpoints A and B). We would want to count the amount leaving Checkpoint A and confirm that it arrived at Checkpoint B. If the two amounts were not the same, this would indicate that we had a problem somewhere along the way between Checkpoint A and B. By counting the amount of air flow at two designated checkpoints on a cable route, we can quickly determine if there is a leak between them. If everything arrives at Checkpoint B, we're home free because there is no leak in that particular section.
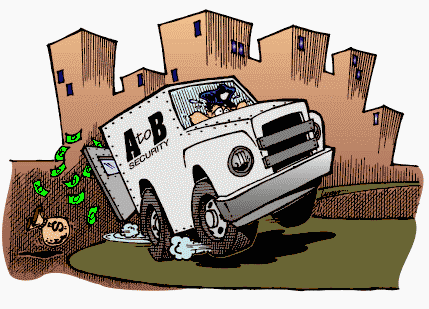
How Is Air Flow Measured?
By far, the most accurate way to measure air flow is to count individual molecules. To make this measurement more manageable, the molecules are measured by the box full. The box size is a standard cubic foot (12" x 12" x 12"), measured at sea level (a point of standard atmospheric pressure). The amount of standard cubic feet consumed is measured either per hour or per day. This measurement lets you measure high consumption rates (air dryer output) or relatively low consumption (air flow into a cable) in a meaningful way, using Standard Cubic Feet per Day (SCFD) or Standard Cubic Feet per Hour (SCFH). These measurements help in monitoring for system leaks and in cable maintenance.Because of maintenance activity, cable splices, and the use of pneumatic fittings along the cable route, all cables tend to leak to some extent. For this reason, an allowable air flow rate, called Optimum Air Usage (OAU) has been established. OAU is the calculated air consumption rate that an air pressure system should use under normal operating conditions. It is based on a consumption rate of 1.25 SCFH per sheath mile of cable.
Like the minimum air pressure standards, OAU is important in dispatching maintenance technicians. A flow increase at an air source is not valuable information unless you also know the OAU, or what the air source should be flowing. OAU is also important in the design of an air pressure system and for evaluating system quality.
What About Air Pressure?
As mentioned previously, most of the air distributed into a cable system is provided by a mechanical air compressor/dryer. This central office equipment compresses or squeezes air molecules together within a given area to create greater air pressure. It's kind of like a garbage compactor in some ways, but with a more useful end result. The amount of compression is measured in Pounds per Square Inch or PSI. For years, PSI readings were the only measurements being used in air pressure maintenance. They're still very important, but nowadays people have come to rely on both pressure and air flow measurements.And What Is Pneumatic Resistance?
Another important concept in cable maintenance is pneumatic resistance. This is the amount of resistance that air flow meets as it moves along inside the cable sheath between conductors. What determines the amount of pneumatic resistance in a particular section of cable are its length, the gauge of the conductors, the type of insulation (PIC or pulp), and the number of pairs in the cable.Pneumatic resistance must be taken into account when using pressure and flow measurements when leak locating along a route. Together these three components comprise the important information needed to perform many of the successful leak locating formulas being used today.