So Why Are Telephone Cables Pressurized?
The biggest threat to telephone wires (conductor pairs) is moisture. Many of the copper cables use paper or pulp as insulation between the individual conductor pairs. This type of cable offers excellent insulation characteristics as long as it is maintained dry. Pulp insulation has been around for a long time, and for many years it had essentially no competition. Eventually plastic insulated conductor (PIC) cable encroached upon its popularity and took over the number-one spot.Unfortunately, the integrity of the protective cable sheath (which is made of lead or polyethylene) is compromised when cracks develop. The cracks in the sheath or associated splice cases allow water to enter and electrolysis to occur, which results in faulted pairs within the cable.
All of us are familiar with moisture damage when the morning paper is left in the rain. The characteristics of the paper change completely with the water damage. This is the same thing that happens inside the cable sheath when water permeates it. The first indication of moisture in a cable is noise on the line, followed by complete cable failure.
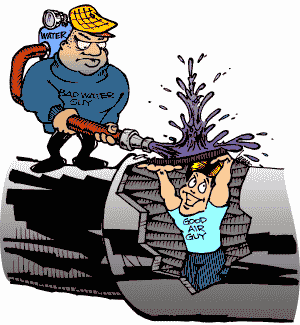
This is the basic premise of cable pressurization: Keep the pressure within the cable in excess of the pressure that could be applied by standing water. To help achieve this objective, telephone companies establish minimum air pressure standards for cables in different environments. For example, an underground cable (one that goes through conduit and utility holes underneath the street) might have a minimum air pressure standard of 5 PSI, enough to protect the cable from approximately 10 feet of water. A direct buried cable requires less air pressure protection (usually 3 PSI) because it is placed only a foot or so below the surface. Aerial cables typically require only 2 PSI because they are at less risk from water damage.
The cable, although filled with individual conductors and associated insulation, is much like a long garden hose carrying air pressure instead of water. The pressure comes from a mechanical air compressor and dryer, located somewhere near the telephone company cable vault. The compressor supplies the air at approximately 10 PSI, while the dryer removes the residual moisture. Essentially, this means that air with very low humidity is forced into the cables.
How Is Air Distributed?
Imagine once again that the cable route is like a garden hose. This hose is made up of different sections that are many thousands of feet long. Depending upon its age and a number of other variables, there will typically be leaks at various points along the cable. Like a hose, the pressure in the cable diminishes as the length increases. The pressure must be re-established in the system along the route, or the cable will be unprotected at substantial distances from the central office. Obviously, finding and fixing all of the leaks in the cable will help considerably. But, with technicians constantly working on cables (opening splices, etc.) and with electrolysis being a constant threat, air pressure must also be raised.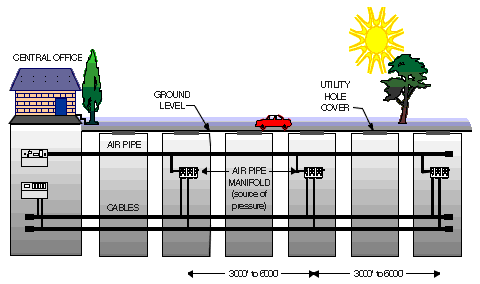
To make sure that adequate delivery pressure is supplied to the cables in the field, most telephone companies set a minimum pipe endpoint pressure standard of 7.5 PSI. If the pipe pressure falls below this standard, cable protection is jeopardized. For example, it's impossible to maintain 5 PSI in an underground cable when the delivery pressure from the air pipe is only 4 PSI. For this reason air pipe delivery pressure must be carefully monitored. Think of it as a main artery in the system. If pressure in the air pipe is low, the whole system is low.